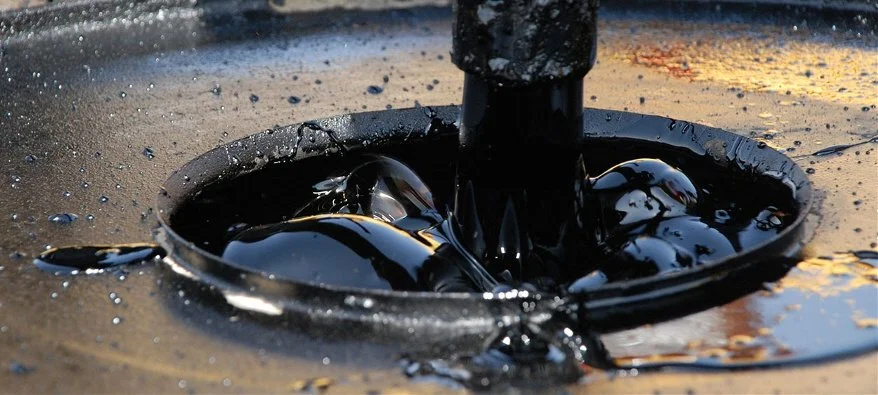
Bitumen Production Process
Table of Contents :
Bitumen production processes.
Distillation Process.
Air Blowing / Aeration Process.
Blending Process.
Bitumen production processes :
Bitumen is produced from the residual fractions obtained during the distillation of carefully selected crude oils. The refining process involves separating the lighter components—such as gasoline, diesel, and kerosene—from the heavier residues that form the base of bitumen.
Depending on the origin of the crude oil and the technological capabilities of the refinery, different methods can be used to manufacture bitumen that meets specific performance requirements. In many cases, a combination of refining techniques is applied to achieve the desired specifications.
Distillation Process :
In the distillation method, crude oil is first heated to temperatures between 300°C and 350°C. This separates the lighter fractions (such as gases, naphtha, kerosene, and diesel) from the heavier non-boiling residue, known as atmospheric residue. This atmospheric residue is then transferred to a vacuum distillation column, where the pressure is significantly reduced (e.g., 0.1 bar) to allow further separation without cracking the molecules. This produces the vacuum residue, which becomes the base for different grades of bitumen. The temperature and pressure conditions inside the vacuum unit play a crucial role in determining the hardness and penetration grade of the resulting bitumen.
In some cases, solvent de-asphalting is used to further separate components without altering their chemical structures. Using solvents like propane or butane, different categories of bitumen can be obtained depending on the desired balance of asphaltenes and maltenes. Bitumen characteristics such as needle penetration and softening point (Ring and Ball method) are used to classify and specify bitumen grades for engineering applications.
Air Blowing / Aeration Process :
The oxidation process, also known as air blowing or aeration, involves passing hot air (at over 200°C) through molten bitumen. This process modifies the bitumen’s physical and rheological properties by increasing the softening point and reducing the penetration value, making it more rigid and durable. There are two outcomes depending on the level of oxidation:
Air-rectified bitumen: Slightly modified, used in paving and some roofing.
Oxidized (blown) bitumen: Highly modified, used primarily in roofing, waterproofing, and industrial sealing.
In semi-oxidation (semi-blown process), compressed air—often mixed with gases such as oxygen, nitrogen, or CO₂—is injected into a reaction tower. The process can be batch or continuous, and the product is a semi-blown bitumen with moderate hardness (e.g., 85/100, 70/60), ideal for road construction and moisture barriers. If the oxidation continues, the penetration decreases further and the softening point rises, resulting in firm oxidized grades such as 110/10, 90/15, or 85/25, which are widely used in building insulation and roofing membranes.
Blending Process :
In addition to distillation and oxidation, blending is another key method of bitumen production. It involves mixing high- and low-viscosity residues in precise ratios to achieve desired performance characteristics :
Blending can occur :
Directly at the refinery
At distribution terminals
Or at third-party facilities, where transportation and distribution are optimized
This process enables the creation of various bitumen types, including :
Hard-grade bitumen: For paving applications
Cutback bitumen: Bitumen diluted with solvents like kerosene, used for cold weather applications
Bitumen emulsions: Suspensions of bitumen in water, stabilized with emulsifiers, ideal for cold mix and maintenance applications
Polymer-Modified Bitumen (PMB): Blends of bitumen with thermoplastics or elastomers to improve elasticity, durability, and resistance to deformation