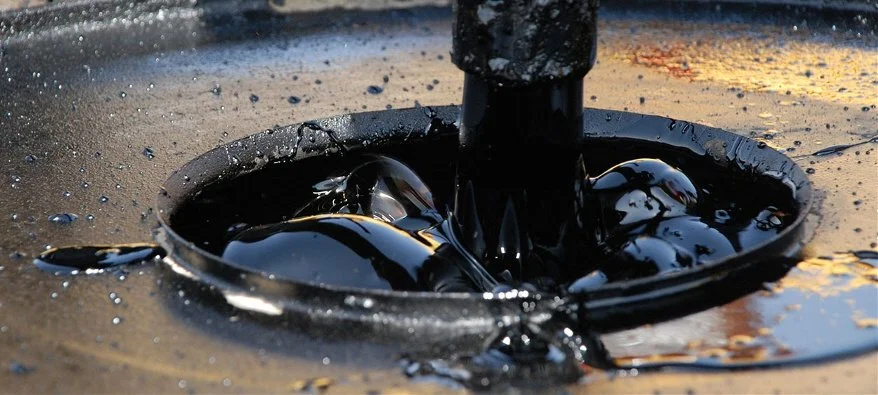
Bitumen Components
Table of Contents :
The bitumen components are classified into four classes of compounds.
Bitumen Components – Chemical Composition.
Physical properties and chemical composition of bitumen.
Temperature susceptibility.
Bitumen Components – Chemical Characterization.
Bitumen Components – Polycyclic Aromatic Hydrocarbons (PAHs).
The bitumen components are classified into four classes of compounds :
Saturates (saturated hydrocarbons): The percentage of saturates is correlated with the softening point of the material.
Naphthenic aromatics: These are partially hydrogenated polycyclic aromatic compounds.
Polar aromatics: These include high molecular weight phenols and carboxylic acids.
Asphaltenes: Comprising high molecular weight phenols and heterocyclic compounds.
Naphthenic and polar aromatics typically represent the major components of bitumen. In addition, natural bitumen usually contains organosulfur compounds, contributing to a total sulfur content of up to 4%. Trace amounts of metals such as nickel and vanadium are also present, typically at concentrations below 10 ppm—similar to certain types of petroleum.
Bitumen is soluble in carbon disulfide and is often described as a colloidal system, with asphaltenes as the dispersed phase and maltenes (a mix of saturates and aromatics) as the continuous phase. Due to the vast number of molecular structures present, it is virtually impossible to fully separate and identify every individual molecule in bitumen.
Bitumen Components – Chemical Composition :
While the chemical components of bitumen are generally similar, they can vary depending on the origin of the crude oil and the specific refining and blending processes used. Bitumen is best described as a complex mixture of hydrocarbons, consisting of a wide variety of high molecular weight chemical compounds. There remains some uncertainty regarding the exact molecular weight distribution of bitumen. The lower end—around 300 Daltons—is defined by the distillation cut point during production. However, the upper limit is still debated: earlier studies suggested molecular weights could reach up to 10,000 Daltons, while more recent research indicates that most molecules likely do not exceed 1,500 Daltons.
The molecular structures found in bitumen include alkanes, cycloalkanes, aromatics, and heteroatomic compounds containing sulfur, oxygen, nitrogen, and trace metals. These heteroatoms introduce slight polarity to the molecules, which plays a key role in the behavior and performance of bitumen. The functionality of bitumen—its ability to interact with other materials such as aggregates or water—is largely influenced by these polar compounds. The presence and nature of such heteroatomic molecules vary depending on the crude source, and they contribute significantly to the physical properties and performance characteristics of the final product.
Physical properties and chemical composition of bitumen :
The bitumen manufacturing processes outlined in Section 3 involve removing lighter fractions, leaving behind high molecular weight compounds with low volatility. As a result, the final products are typically solid or semi-solid at ambient temperature and gradually soften as the temperature rises. The vapor pressure of in-situ bitumen is so low that it falls below the detection threshold of standard instruments. To enable transport and handling, bitumen is usually heated to temperatures above 140°C (284°F) to reach a liquid state. While some performance-related physical properties are governed by national or international standards, others—such as specific gravity or vapor pressure—are inherent outcomes of the production process used to meet those specifications.
Temperature susceptibility :
To ensure performance across a wide range of ambient temperatures, it is important for certain bitumen products to have reduced temperature susceptibility. Various methods are available to evaluate how bitumen properties change with temperature—typically by measuring variations in physical characteristics such as stiffness or penetration. One widely used method in Europe is the Penetration Index (PI). Oxidation of bitumen alters the relationship between penetration and softening point, thereby reducing temperature susceptibility and leading to a systematic increase in the PI of the oxidized material. As such, PI serves as a reliable indicator of the degree of oxidation. However, other techniques are also available to assess the temperature susceptibility of bitumen.
Bitumen Components – Chemical Characterization :
Bitumen is a viscoelastic material, making chemical polarity a key parameter in characterizing its properties. The most polar components contribute to the material’s structural integrity and stiffness (modulus), while the least polar compounds are responsible for its flexibility and performance at low temperatures. Components with intermediate polarity help to stabilize and compatibilize both the polar and non-polar constituents within the bitumen matrix.
Given the continuous and complex distribution of molecules in bitumen, analyzing each individual compound is impractical. As a result, bitumen is typically divided into four main fractions based on increasing polarity:
Saturates, Aromatics, Resins, and Asphaltenes (SARA).
Asphaltenes are generally isolated through solvent precipitation.
The other three fractions—saturates, aromatics, and resins—are typically separated using chromatographic techniques.
Several standardized methods exist for separating bitumen into these four fractions. However, it is important to note that the names of the SARA fractions do not directly reflect their precise chemical composition, which can vary significantly depending on the source of the bitumen.
Bitumen Components – Polycyclic Aromatic Hydrocarbons (PAHs) :
Polycyclic Aromatic Hydrocarbons (PAHs) are of particular interest due to their potential health impacts. PAHs belong to a broader class of compounds known as Polycyclic Aromatic Compounds (PACs), which may also include atoms such as sulfur, oxygen, and nitrogen.
Crude oil naturally contains low concentrations of PAHs, and a portion of these ends up in bitumen at trace levels (typically in the ppm range). However, the temperatures used during bitumen production, which remain below 385 °C (725 °F), are not high enough to generate significant quantities of PAHs. Substantial PAH formation requires pyrolysis or combustion, processes that occur at temperatures above 500 °C (930 °F).
The primary method used to produce bitumen—vacuum distillation—effectively removes most PAHs. Additionally, further processing such as air-blowing (oxidation) has been shown to reduce PAH concentrations even more. During oxidation, bitumen undergoes chemical changes observable in SARA analysis:
• Aromatics are partially converted into resins
• Resins are further transformed into asphaltenes
As a result, the bitumen becomes stiffer and more elastic, with increased asphaltene content and decreased levels of naphthenic and polar aromatics. Once the concentration of asphaltenes exceeds a certain threshold, the bitumen transitions from a viscoelastic material to one that behaves almost purely elastically at ambient temperature.
The oxidation process also introduces oxygen-containing functional groups into the bitumen, including hydroxyl, peroxide, carbonyl, ketones, acids, acid anhydrides, and esters. At the same time, volatile compounds are partially removed. Altogether, these changes contribute to a reduction in PAH content, enhancing the environmental and health profile of the final bitumen product.